Plastic extrusion for creating standardized, premium parts
Plastic extrusion for creating standardized, premium parts
Blog Article
Comprehending the Essentials and Applications of Plastic Extrusion in Modern Production
In the realm of modern-day manufacturing, the method of plastic extrusion plays an instrumental function - plastic extrusion. This intricate procedure, entailing the melting and shaping of plastic with specialized passes away, is leveraged throughout various markets for the development of diverse products. From vehicle components to consumer items packaging, the applications are huge, and the capacity for sustainability is just as excellent. Unraveling the basics of this process discloses real convenience and potential of plastic extrusion.
The Principles of Plastic Extrusion Refine
While it might appear complex, the fundamentals of the plastic extrusion process are based on fairly uncomplicated principles. It is a production procedure in which plastic is melted and afterwards shaped into a continual account with a die. The raw plastic material, frequently in the kind of pellets, is fed right into an extruder. Inside the extruder, the plastic is subjected to warmth and stress, triggering it to melt. The molten plastic is then forced through a shaped opening, referred to as a die, to create a long, continual item. The extruded product is cooled and then cut to the wanted size. The plastic extrusion process is extensively utilized in numerous industries because of its cost-effectiveness, performance, and flexibility.
Different Kinds of Plastic Extrusion Methods
Structure upon the fundamental understanding of the plastic extrusion procedure, it is essential to check out the numerous techniques associated with this manufacturing technique. Both primary methods are profile extrusion and sheet extrusion. In account extrusion, plastic is melted and formed right into a continuous account, typically made use of to produce our website pipelines, poles, rails, and window frames. On the other hand, sheet extrusion produces large, flat sheets of plastic, which are commonly further processed right into items such as food product packaging, shower curtains, and auto components. Each technique needs specialized machinery and exact control over temperature and pressure to make sure the plastic keeps click to read more its form during air conditioning. Recognizing these strategies is vital to utilizing plastic extrusion effectively in modern manufacturing.
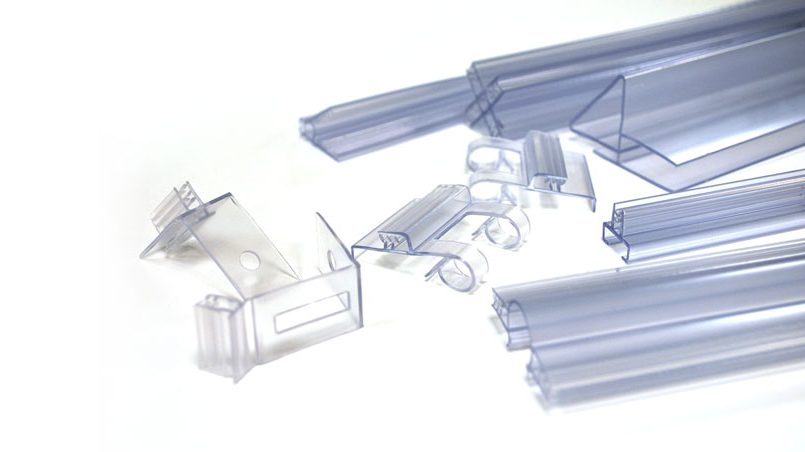
The Role of Plastic Extrusion in the Automotive Market
An overwhelming bulk of components in modern-day vehicles are products of the plastic extrusion process. Plastic extrusion is mainly utilized in the manufacturing of numerous auto components such as bumpers, grills, door panels, and dashboard trim. Therefore, plastic extrusion plays a crucial duty in auto manufacturing.
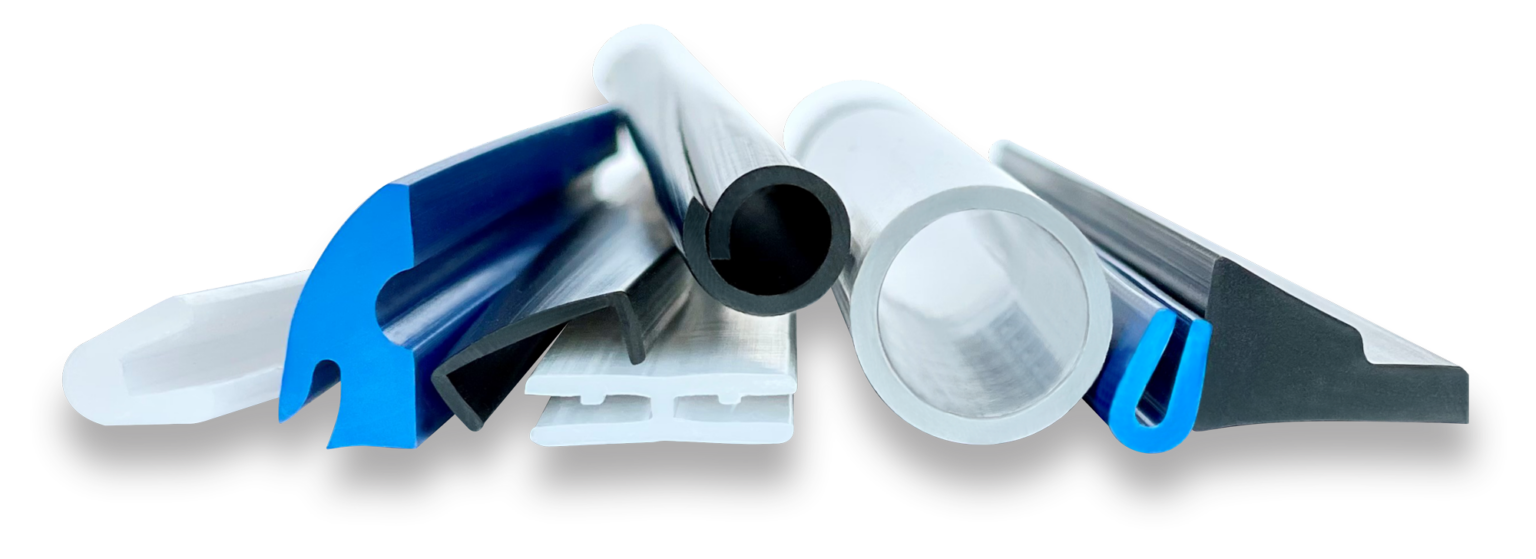
Applications of Plastic Extrusion in Durable Goods Manufacturing
Beyond its substantial effect on the auto industry, plastic extrusion verifies equally efficient in the world of consumer goods making. The adaptability of plastic extrusion permits manufacturers to make and produce complicated shapes and dimensions with high accuracy and efficiency. The flexibility, flexibility, and cost-effectiveness of plastic extrusion make it a recommended choice for several customer goods producers, adding dramatically to the industry's growth and advancement.
Ecological Effect and Sustainability in Plastic Extrusion
The pervasive use of plastic extrusion in making invites examination of its environmental implications. Efficient machinery lowers energy use, while waste management his response systems reuse scrap plastic, lowering raw product needs. In spite of these improvements, even more development is required to mitigate the environmental impact of plastic extrusion.
Conclusion
In final thought, plastic extrusion plays an important function in contemporary manufacturing, particularly in the vehicle and customer items markets. Recognizing the essentials of this process is crucial to enhancing its applications and advantages.
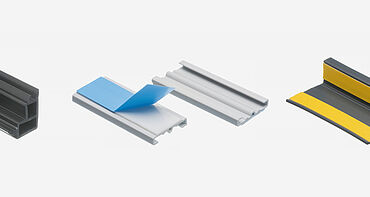
The plastic extrusion procedure is thoroughly used in numerous markets due to its flexibility, cost-effectiveness, and performance.
Building upon the fundamental understanding of the plastic extrusion process, it is essential to discover the numerous strategies involved in this production technique. plastic extrusion. In contrast, sheet extrusion produces big, level sheets of plastic, which are generally additional refined right into items such as food product packaging, shower drapes, and automobile parts.A frustrating majority of parts in modern-day lorries are products of the plastic extrusion process
Report this page